Studio Other recently completed a project for Boston Consulting Group (BCG), which involved 685 custom-designed workstations for the new headquarters. An issue arose because each desk included an arched eight-foot panel, making it space inefficient in terms of shipping, and therefore, costly for the east coast client. Refusing to accept the price as is, Studio engineers put their heads together to find a cost-effective solution. After testing several different shipping methods, Studio Engineer Jeremy Knapp found the answer in a double-stacked pallet.
The seven-foot wide pallet contained spacers on either side and pool noodles to stack two pallets on top of one another with the entire unit shrink wrapped for scratch protection. The measurements were calculated strategically, as there were only 4-inches of margin on each side of the workstation. Because of this method, Studio was able to cut the original estimated 19 tractor trailers down to only eight, with each 53-foot truck able to hold 40 workstations. Thanks to Studio engineering innovation and persistence, the team saved BCG a significant sum of money in shipping costs.
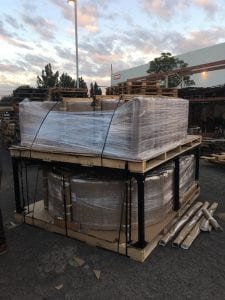
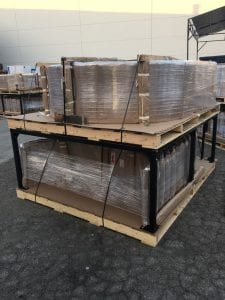
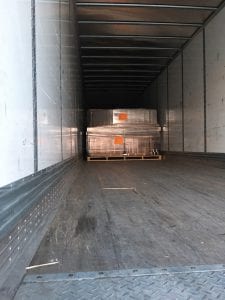